Risk or opportunity?
Skills shortage in production planning: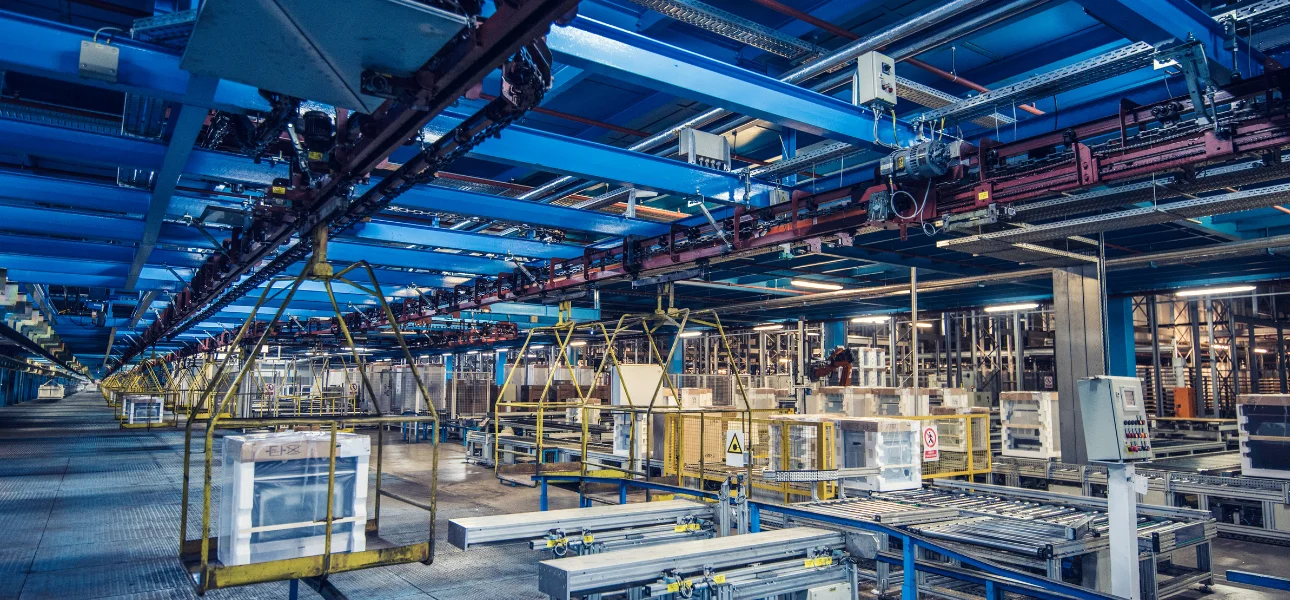
It is not a new realization that I am coming to more and more frequently: the shortage of skilled workers is no longer a gloomy future scenario, but a bitter reality. The lack of qualified specialists is also becoming increasingly noticeable in production and specifically in production planning. Without well-trained and satisfied staff, production processes become inefficient, leading to bottlenecks, delays and higher costs. But is the shortage of skilled workers really just a risk - or could it also lead companies to take new, innovative paths, optimizing their planning and existing production processes to remain competitive?
Attention, spoiler: I believe that the shortage of skilled workers offers us opportunities on many levels. Both for individual companies and for Germany and Europe as a business location. But first I would like to briefly list the (certainly not unknown) risks that the shortage of skilled workers entails, especially for manufacturing companies.
Skills shortage - a problem with far-reaching consequences: Statistics show that even in production planning, as I have mentioned in detail, numerous positions remain unfilled. The “war for talent” has hit the manufacturing industry hard. Small and medium-sized enterprises (SMEs) are particularly affected, as they often do not have the resources to keep up with the competition for the best minds. But what specific risks does the shortage of skilled workers in production planning actually entail?
Risks of the skills shortage:
- Bottlenecks in production: a lack of planners can lead to production processes running sub-optimally. This causes bottlenecks which, in the worst case, can paralyze the entire production process. Unplanned machine downtimes, an increase in set-up processes and the associated waste of resources are frequent consequences.
- Decrease in employee satisfaction: Faulty and unpredictable production planning and the resulting perceived chaos in production are eating away at employee satisfaction - beyond production planning. Employees are increasingly distracted from the actual work they enjoy doing. Dissatisfied employees mean one thing above all: the actual efficiency of production is drastically reduced.
- Delays in the supply chain: Inefficient planning inevitably leads to delays in the supply chain. Customers cannot be supplied on time, leading to dissatisfaction and, in the worst case, the loss of important customers. In a world where just-in-time deliveries and greatly reduced storage times have become the norm in many industries, this can have fatal consequences.
- Cost explosion: Every mistake in planning usually results in additional costs - be it through overtime, the use of expensive replacement solutions or penalties for late deliveries. A lack of skilled workers makes it difficult to avoid such mistakes and to compensate for errors that do occur.
- Competitiveness at risk: Companies that do not have their production processes under control risk falling behind in national and global competition. In times when markets are increasingly competitive, this can make the difference between success and failure.
Opportunities through new strategies: However, the shortage of skilled workers is also forcing companies to rethink their usual strategies and explore new avenues. Two particularly promising approaches have emerged: the outsourcing of production planning and the introduction of specialized production planning software.
1. Outsourcing production planning: Outsourcing company processes is no longer a new concept, but it is still little used in production planning. Yet it offers numerous advantages, especially in times of skills shortages.
Advantages of outsourcing:
- Cost efficiency: by outsourcing production planning, companies save on the costs of recruiting and training skilled workers and investing in their own planning tools. Instead, they only pay for the planning services actually provided.
- Access to expertise: External service providers specialize in production planning and often bring in-depth expertise that would be difficult to build up internally. This allows companies to benefit from proven best practices and innovative solutions without having to develop them themselves.
- Flexibility: Another advantage of outsourcing is flexibility. Companies can decide how much they want to outsource depending on the order situation. This allows resources to be used optimally and planning bottlenecks to be avoided.
- Focus on core competencies: By outsourcing their production planning, companies can focus more on their core competencies. The internal team is relieved and can focus on strategic tasks.
Outsourcing risks: Of course, there are also challenges. These include dependence on external partners and the need to share sensitive data. Trust and clear contractual agreements are crucial here to ensure smooth processes. Communication must also be right so that no misunderstandings arise.
2. Introduction of production planning software: An alternative strategy for overcoming the shortage of skilled workers is the introduction of specialized production planning software (PPS) or an advanced planning system (APS). These tools are designed to make production processes more efficient and transparent.
Advantages of software solutions:
- Automation and efficiency: production planning software automates many repetitive tasks that would otherwise have to be done manually. This increases efficiency and minimizes planning errors.
- Transparency and control: With the right software, companies have insight into their production processes at all times. They can identify bottlenecks at an early stage and take countermeasures. In addition, important key figures can be monitored in real time, which improves decision-making.
- Scalability: Software solutions can be flexibly adapted to growing requirements. As the company grows, the software can be easily expanded without the need to hire new planners.
- Integration: Modern production planning software can be integrated into existing systems such as MES (Manufacturing Execution Systems) or ERP (Enterprise Resource Planning). This ensures a smooth flow of data and avoids duplication of work.
Challenges during implementation: However, the introduction of new software is not without its challenges. Companies must be prepared to invest in the implementation and training of their employees. In addition, existing processes need to be partially adapted to the new software, which requires time and resources. Regularly updating and adapting the software to new processes along the value chain is also necessary in order to keep pace with changing market conditions.
Conclusion: The shortage of skilled workers in production planning is undoubtedly a major risk. However, as I mentioned so often at the beginning, this challenge also presents opportunities for companies that are prepared to break new ground. Whether through outsourcing or the use of modern software solutions, companies today have more opportunities than ever to optimize their production processes and position themselves for the future - a clear break with the “We've always done it this way!”. In my opinion, the key lies in finding the right solution for your own company and implementing it consistently.
Ultimately, it's about seeing the shortage of skilled workers not just as a threat, but as an impetus for change and innovation. With the right measures, the shortage of skilled workers can even become an opportunity, e.g. to take your own production planning and therefore your own production to the next level.