Production Planning and Manufacturing Execution
double foundation: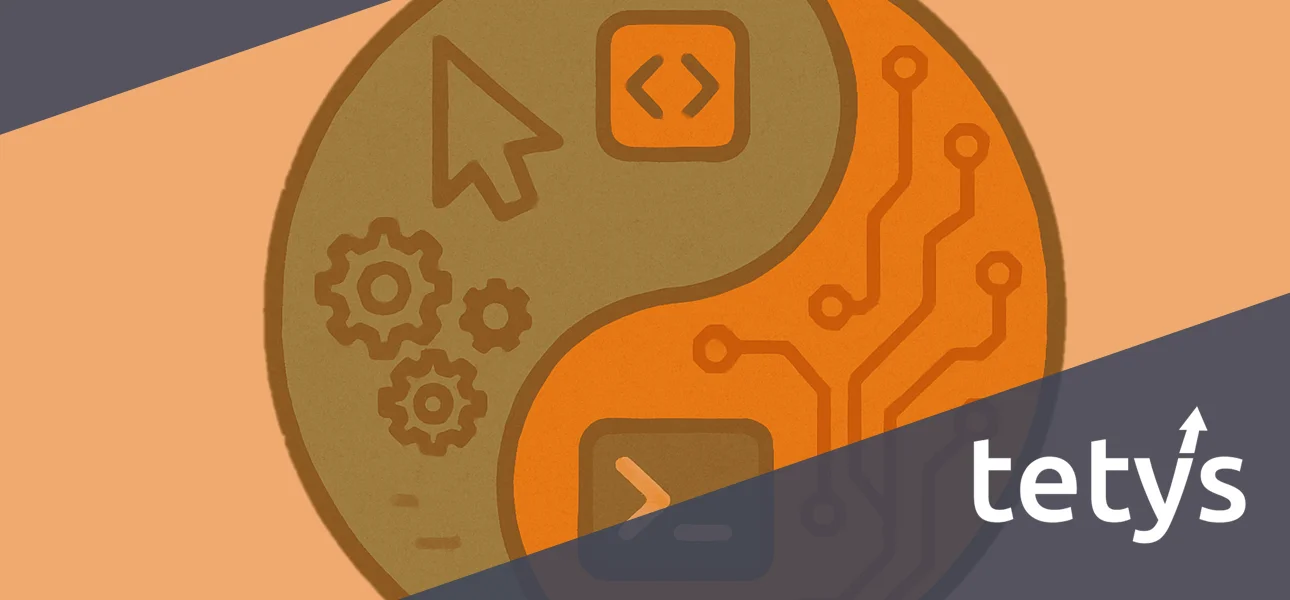
Production Planning and Scheduling
Today, digital production planning is primarily implemented using PPS (Production Planning and Control Systems) and APS (Advanced Planning and Scheduling) software solutions. These systems are responsible for defining the "target" of production – that is, the optimal planning of resources, materials, machines, and personnel.
An example of such a solution is our planning tool FEKOR. It helps companies fulfill customer orders on time and cost-effectively. Both materials management (disposition and provision of materials, assemblies, and finished goods) and production planning (workflows in manufacturing) are taken into account.
Key objectives of digital planning include meeting delivery deadlines while minimizing production costs. In case of conflicts, delivery readiness is prioritized over cost efficiency. Planning takes place on two levels:
- Rough planning is often still handled by traditional ERP systems, but these are frequently too slow and imprecise for short-term decisions.
- Detailed planning is increasingly managed by specialized systems like FEKOR, which are capable of creating realistic and executable plans – without double bookings and with high flexibility.
Manufacturing Execution System
Digital production control is implemented using so-called MES (Manufacturing Execution Systems). These systems form the interface between the planning level and the actual production environment, known as the shop floor.
An MES system enables direct integration of machines into the IT system. This allows operating states and production data to be automatically recorded and processed in real time, forming the basis for precise and up-to-date control of manufacturing processes.
Another key aspect is the recording of process cycles. MES systems continuously document and analyze production workflows, enabling complete traceability and process optimization.
Quality control is also supported by MES systems. Inspection processes can be integrated directly into production, allowing quality data to be captured and evaluated during manufacturing. This significantly reduces scrap and rework.
In addition, MES systems continuously collect so-called actual data – the real-time status of production. These data provide a solid foundation for informed decision-making and enable quick responses to deviations from the plan.
Another advantage is the paperless design of machine workstations. Work instructions, drawings, and inspection plans are provided digitally, which not only increases efficiency but also reduces sources of error.
Our tetysMES, together with our WebGT as a universal user interface for your shop floor personnel, serves as a central hub at workstations in your production. It connects machine operators with their immediate environment by exchanging information with peripheral devices, automated guided vehicles (AGVs), forklifts, and warehouse systems. This creates an intelligent, networked production environment that can respond flexibly and efficiently to changes.
MES and PPS – Firmly Anchored in Operations
A key benefit of combining both systems is the feedback loop: The originally created target plan is enriched with real-time actual data from the MES system. This results in a dynamic system that can be optimized with great agility.
For example, it becomes easy to identify when certain machines consistently take longer for specific orders than planned. These insights flow directly into the next planning cycle – making the planning more realistic, robust, and efficient.
Another advantage of integration is the live overview of all relevant production data. Production managers and planners gain real-time insights into:
- Machine statuses
- Order progress
- Quality metrics
This transparency enables quick responses to disruptions, such as machine downtimes or material shortages. At the same time, it reveals potential improvements and bottlenecks, allowing for targeted process optimization.
The combination of digital production planning and control offers numerous benefits. It increases delivery reliability by enabling early detection and correction of deviations from the plan. At the same time, production costs are reduced through more efficient use of resources and the avoidance of overproduction.
The systems also allow for flexible responses to short-term changes and improve the utilization of machines and personnel. Moreover, the end-to-end transparency across all production processes supports better decision-making and continuous optimization.
The integrated system of FEKOR and tetysMES is a prime example of how this integration works in practice. It not only handles planning but also continuously adapts and controls production processes.
If you would like to learn more about these topics, feel free to contact our experts directly. Let’s explore together how we can sustainably embed your production planning and control processes into the digital world.
We look forward to learning about your requirements and are happy to support you with our solutions.
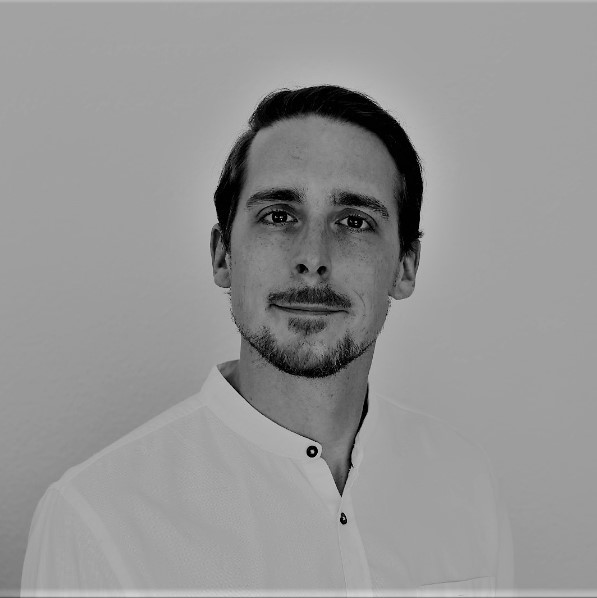