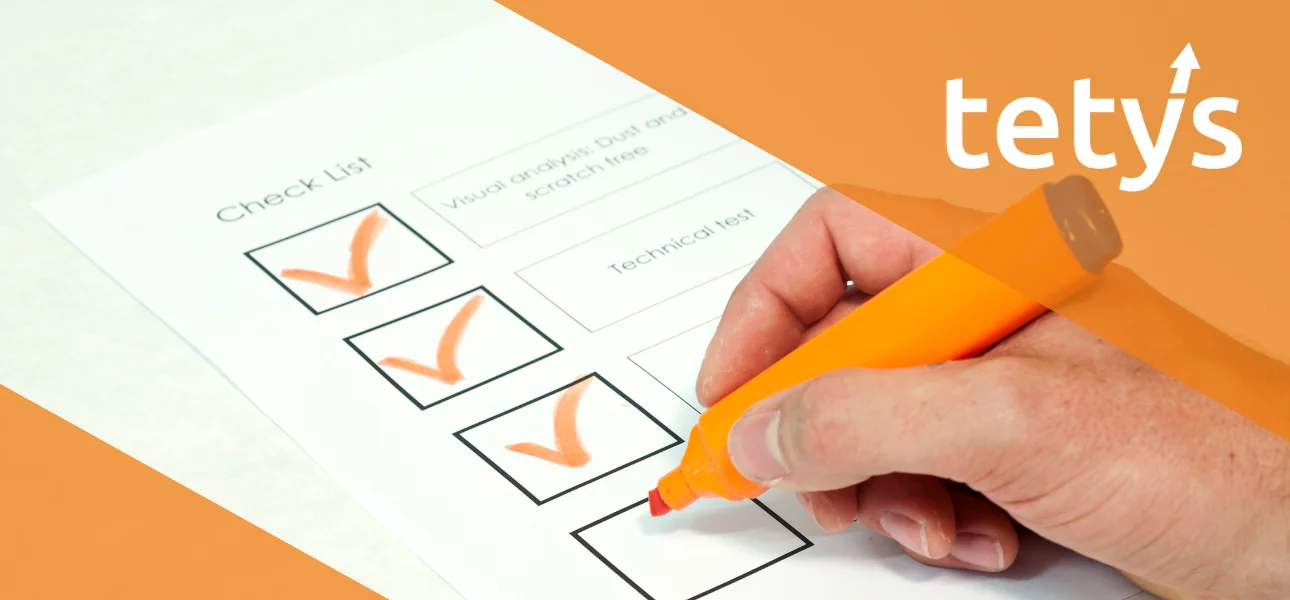
Quality management in production / Reasons to invest in quality measures
What do e-coli bacteria in sausages, small parts on children's toys that can be swallowed and cracks in bicycle helmets have in common?
They are all product recalls! Negative press and loss of consumer confidence included.
That stays in your memory and burns itself in! Who doesn't remember the exploding Samsung smartphones? The whole thing happened 9 years ago and yet it immediately came back to me.
Costs have to be cut in production and everything has to be manufactured as quickly and cheaply as possible so that you can keep up with the competition and not go under. But shouldn't we rethink our approach and focus on quality for this very reason?
Made in Germany was long regarded as THE mark of quality. And especially today, when it feels like it is a rarity if something is still made in Germany, we should pay even more attention to the quality of these products!
The demands on manufacturing companies are increasing all the time: shorter delivery times, legal requirements and rising customer expectations. This makes professional quality management a decisive success factor when it comes to competition and future-proofing a company.
What is quality management in production?
Quality management encompasses everything that can contribute to the continuous improvement of products and processes. In production, this includes reducing waste, avoiding errors and increasing customer satisfaction. This can only be achieved if you plan, monitor and control every step and process from order placement to raw material procurement and delivery. Of course, the best way to do this is with the right software.
The most important reasons to invest in quality measures
- Increased customer satisfaction and strengthening of the brand image
After my introduction, this point is almost self-explanatory. Customers expect flawless, durable and reliable products. If you meet these expectations (or even exceed them), you create trust and bind customers to the company in the long term. Satisfied customers buy more and recommend you to others. This ensures stable sales and strengthens the brand image.
- cost savings through fewer rejects and rework
Errors cause high costs. Whether through rejects, rework, recalls or late deliveries. You can therefore save money, time and materials if you use effective quality management to detect errors at an early stage or even prevent them. Today, there are many clever software solutions for and especially in the prevention of errors, A.I. plays an increasingly important role.
- compliance with legal requirements and competitive advantages
Numerous regulations and standards apply in the industry. With a good system, you can reliably meet these requirements and avoid recalls or fines. Customers and partners are also increasingly demanding proof of quality. Certified quality management systems in particular, such as ISO certification, are a prerequisite in some sectors in order to be able to participate in the market at all! There is no better proof that quality and reliability are important. This gives you a clear competitive advantage!
- more efficient processes and higher production
Quality management helps to create standardized processes and procedures and therefore more transparency. This not only makes work easier, but also speeds up production and increases efficiency. Not only can errors be identified and rectified more quickly, but potential for improvement can also be discovered and implemented.
- greater employee involvement and better error culture
The new processes and greater transparency allow employees to get more involved. This promotes a general quality mindset and an open, constructive error culture. This promotes cooperation and puts us in a good position for the future.
Conclusion: Quality is no coincidence - it is the result of targeted investment
The demands placed on manufacturing companies today are very demanding and diverse. Customers expect flawless products to the highest standards, reasonable costs, on-time delivery and, ideally, sustainable business practices. And companies are under pressure to deliver all this while being efficient and saving costs. At this point it becomes clear: quality management is not a “nice-to-have” but a central building block for long-term corporate success.
Investments in quality measures pay off in many ways: They help to minimize sources of error and reduce rejects and rework. This increases costs and boosts the efficiency of the entire value chain. This creates trust and strengthens the brand image.
Quality management also promotes an open error culture and therefore employee participation. Experience and ideas lead to innovation and continuous improvement. Modern software solutions can help to record and evaluate quality data in real time and derive targeted measures. This is an advantage for anyone who wants to act in an agile and future-oriented manner.
Another positive effect is that structured quality management can help to meet legal and regulatory requirements and minimize risks such as production recalls and reputational damage. Investments are therefore not a short-term expense, but a sustainable strategy to equip the company for future challenges.
Investing in quality today lays the foundation for success tomorrow.
